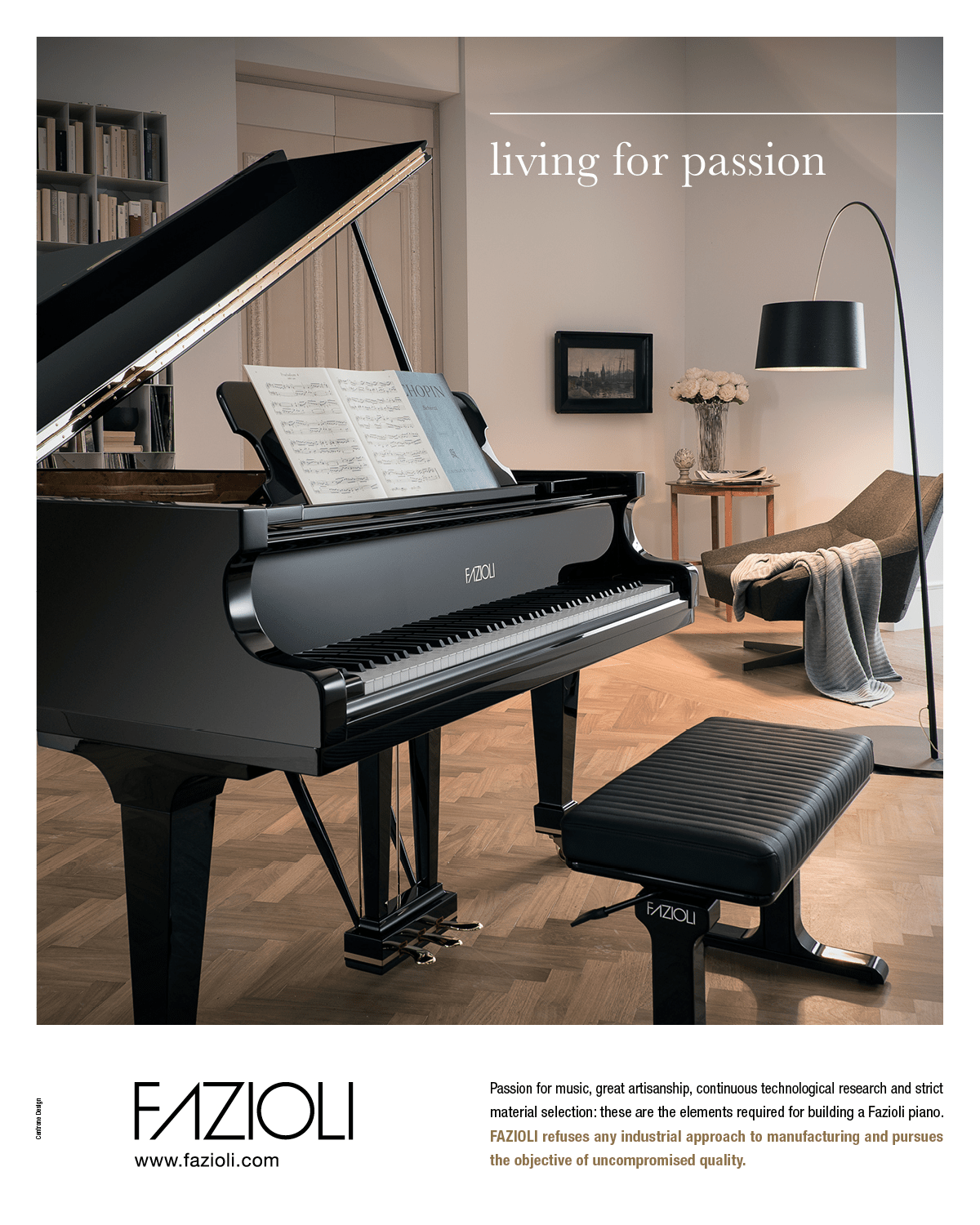
The Definition of Quality
In the manufacture of medium-grade pianos, the term quality typically refers, in large part, to quality control; that is, that each example of a particular model is exactly like every other example. So, in theory, a model could have a satisfactory but unexceptional tonal design, and use satisfactory materials that meet structural specifications, and if all the pianos of that model are made to the same standards, the model could be considered to be of good quality.
In the manufacture of high-end pianos, however, quality means something more: Each instrument is judged not on its similarities to other examples of the same model, but on its excellence as a unique musical instrument. In fact, because the natural materials that pianos are made from are never completely uniform, and because the craftspeople who make these instruments are trained to maximize the musical potential of each instrument, any particular model of high-end piano is likely to exhibit small variations in performance characteristics from instrument to instrument.
• • •
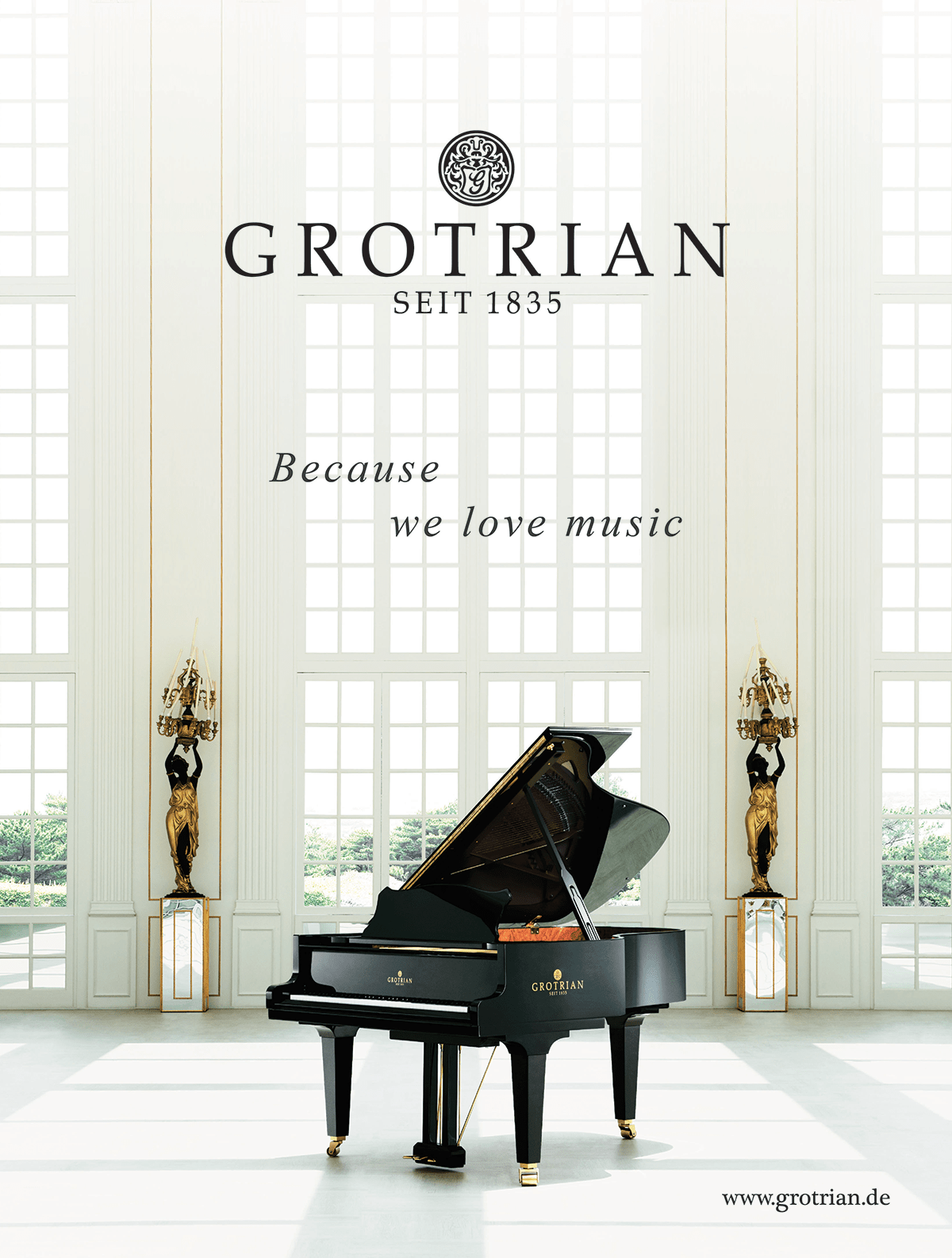
So what do serious pianists, piano owners, piano technicians, and administrators of institutional music programs look for and expect in a high-end piano?
Tonal Quality
A piano with a singing tone, long sustain, and a wide dynamic range gives the pianist more latitude in creating musically expressive performances. The length of an instrument’s sustain is essential to the pianist’s ability to make it “sing” in passages that require one note to connect with the next. In addition, the ability of a concert instrument to project to the back of today’s large halls is critical to its success. Although a piano’s tonal color (harmonic content) will vary depending on the tonal philosophy of the manufacturer, it should be consistent from note to note within each register, and transition smoothly from register to register across the instrument’s entire range. Playing with different levels of force should produce predictable variations of tonal color and volume (see “Action Control,” below). Professional pianos excel in these regards, and the technician’s ability to artistically voice an instrument to bring out these elements of tone depends on the excellence of the soundboard wood, the rim stock, and the hammers.
At first, customers may feel they can’t hear the difference between fine instruments and less-expensive models, but this is easily remedied with more exposure to the better instruments. Listen carefully to recordings, live concerts, and fine instruments at educational institutions, and your ear will begin to hear the difference.
Action Control
There are many opinions about the extent to which a pianist can affect the tone of a piano while playing, but it is a fact that, with the more sensitive actions of high-quality instruments, the skilled pianist is able to more reliably control the speed of the hammers’ attack on the strings, and thus create a wider tonal palette, giving the audience a better and more nuanced musical experience. This is readily apparent at international piano competitions, at which many pianists, playing the same works on the same piano, can nonetheless bring forth very different tonal qualities from it. The ultimate experience of action control for the artist, possible with only the finest instruments, occurs when the piano becomes a seamless extension of the pianist’s thoughts and feelings — the action seems to disappear, the music seeming to rise effortlessly from the instrument without the presence of an intervening mechanism.
Amateurs also benefit by discovering that many concepts discussed by more advanced pianists, such as phrasing, legato playing, and fast and reliable repetition, are now achievable when playing actions of more sophisticated design, longer keys, and parts that can be regulated more accurately.
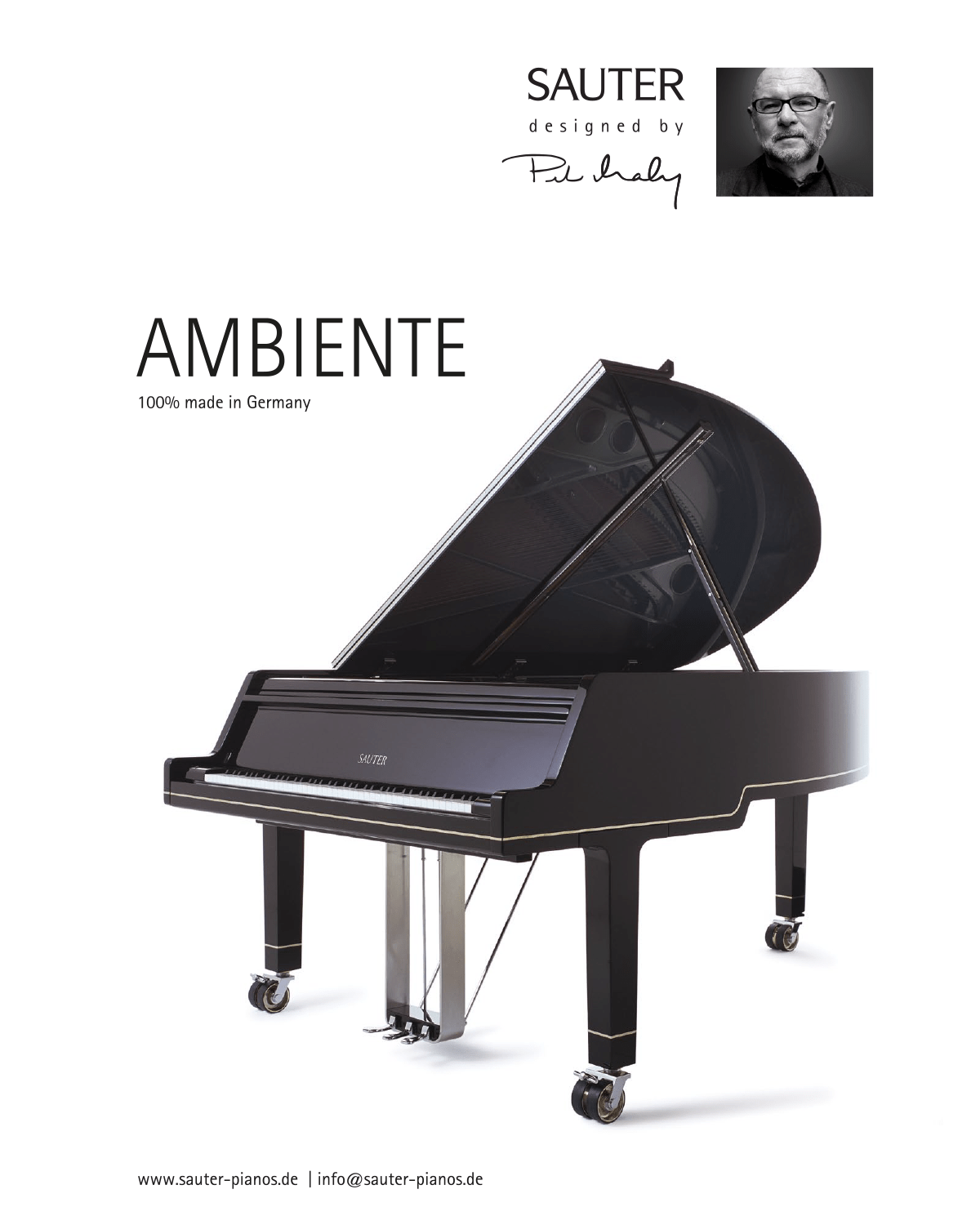
Service and Maintenance
Because high-end pianos are more musically sensitive than less costly ones, they may require more frequent servicing if they are to be kept at peak performance levels. But this doesn’t necessarily mean that they’re delicate and finicky. Most of these expensive instruments are built to be taken down, moved, and set up constantly; played with vigor for many hours a day; and tuned and serviced regularly. In my experience, after an initial settling-in period, and a good regulation and tuning, high-end pianos are actually easier to maintain than less costly ones, requiring only slight touch-up adjustments on a regular basis. This comes as a surprise to many shoppers who are concerned that the maintenance of these instruments will be costly.
The reason is that high-end pianos usually have designs and materials that make their tuning and servicing easier, more accurate, and more stable. The woods used are more carefully chosen and processed with consideration for their ability to resist environmental changes, and more robust and careful construction of the piano’s structural elements result in greater tuning stability and longevity. The action regulation and voicing are more likely to be stable because of better musical preparation at the factory, and higher qualities of cloth and felt in the action and hammers. More careful design and detailing of the piano at the factory mean fewer annoying problems to deal with later on.
• • •
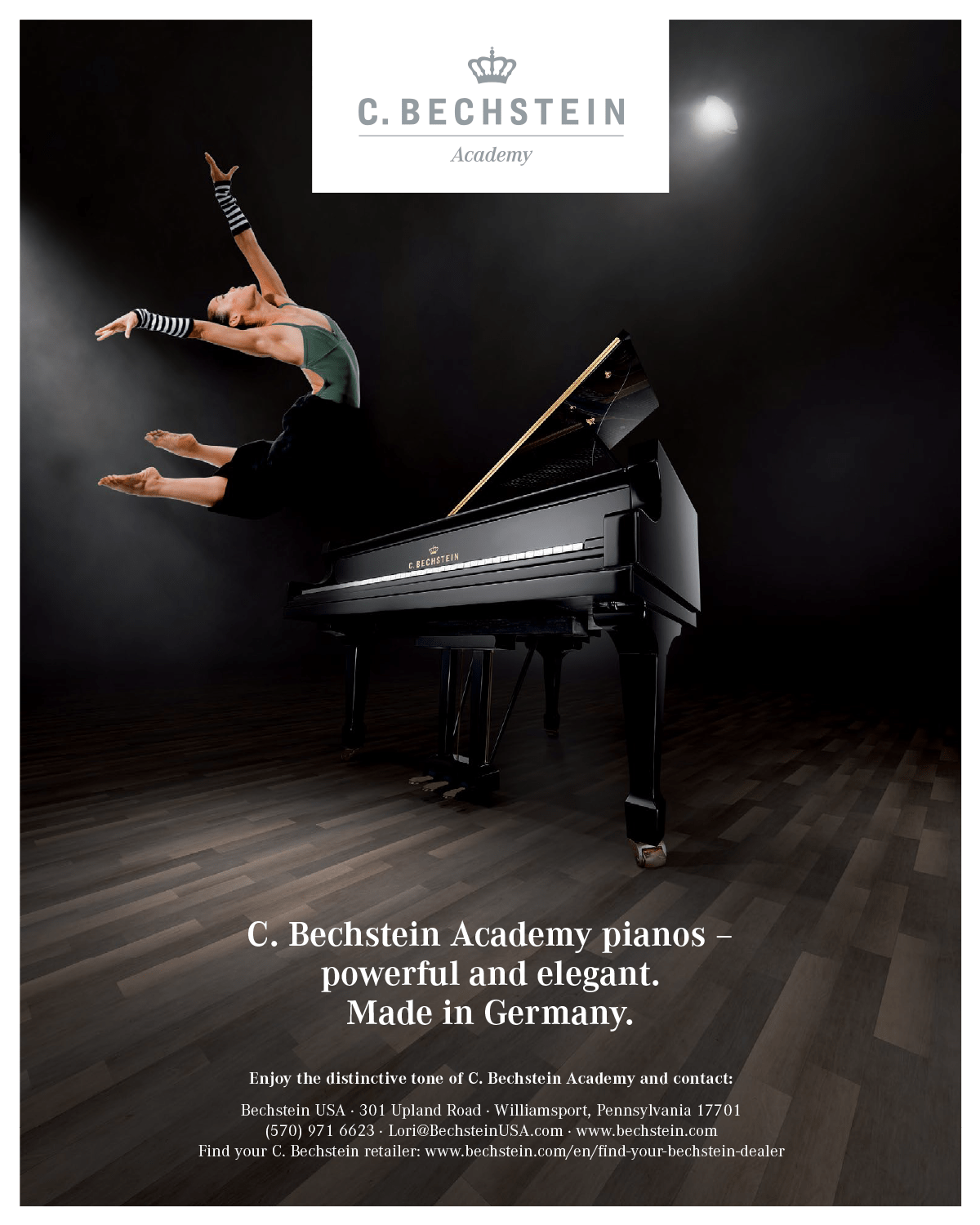
High-performance pianos are much more expensive than consumer-oriented models because they are so much more costly to build. Moreover, when these higher costs, along with overhead and profit, are spread over the smaller demand for this type of piano, the cost difference per instrument is greatly magnified. In the manufacture of the best pianos, few economies of scale are available.
Materials
Many of the woods used in making high-end pianos — e.g., spruce, sugar pine, hard rock maple, beech, hornbeam, ebony, poplar, and rosewood — are chosen for specific properties: ability to transmit sound, strength-to-weight ratio, density, straightness of grain, etc. Woods used for components that will be visible to the buyer, such as soundboards and case veneers, must be visually flawless as well. High-end piano hammers will have tighter specifications for the wool used in their felt, as well as for their construction, to more predictably produce the tonal goals of that manufacturer. In less-expensive instruments, substitutions of less costly materials can often be made that will still result in instruments that are satisfactory for their less-demanding, intended use. But in a premium instrument, any such substitution that would compromise the piano’s tone, stability, longevity, or appearance cannot be tolerated. Because makers of high-end pianos demand only the very best from their suppliers of parts and materials, but do not buy in large volume, they have little leverage over prices, which continue to rise as the choicest natural materials become more scarce.
The refinements of seasoning and quartersawing wood add more cost, but are necessary for maximum stability and longevity. Logs must be air dried for years, then kiln dried to a specific moisture content, so that the wood won’t warp, twist, and crack later on, after installation in a piano. Quartersawing is a method of cutting boards from logs such that the grain is oriented in a direction that results in greater dimensional stability. However, it is a very inefficient use of the log, much of which cannot be used and thus is wasted. While all piano makers season and quartersaw wood to some extent, high-end makers are more fastidious in their selection and use of lumber. This contributes to pianos whose tunings and action regulations are more stable, even when in constant use in practice rooms, teaching studios, and recital halls, and under varying climatic conditions. Less-expensive pianos made primarily for home use won’t survive such conditions nearly as well.
High-end companies use the same materials in all sizes of piano they make, with no compromises on the smaller pianos. This results in very expensive smaller grands and verticals.
Some less-costly brands claim that they use the same parts or materials that high-end brands do. Even when this is technically true, there can be a world of difference in how those materials are processed and/or the parts installed. For example, some less-costly brands advertise that they use the same Renner parts in their actions as are found in some high-end brands. But the high-end companies usually disassemble the parts and reassemble them to their own, stricter specifications, then custom-install them in the pianos, taking into account slight variations in the instruments that require slight repositioning of the parts. This process is too time-consuming and expensive for lesser brands, and may call for expertise that their workers simply don’t have; they’re more likely to use the parts just as they come from Renner, and install them according to a general formula. While this results in instruments that are good enough for most purposes, and perhaps better than those that use lesser-quality parts, it may not allow the actions to be regulated accurately enough for the most musically demanding uses. This example also highlights the error consumers make when comparing brands solely on the basis of features, specifications, and/or lists of parts and materials.
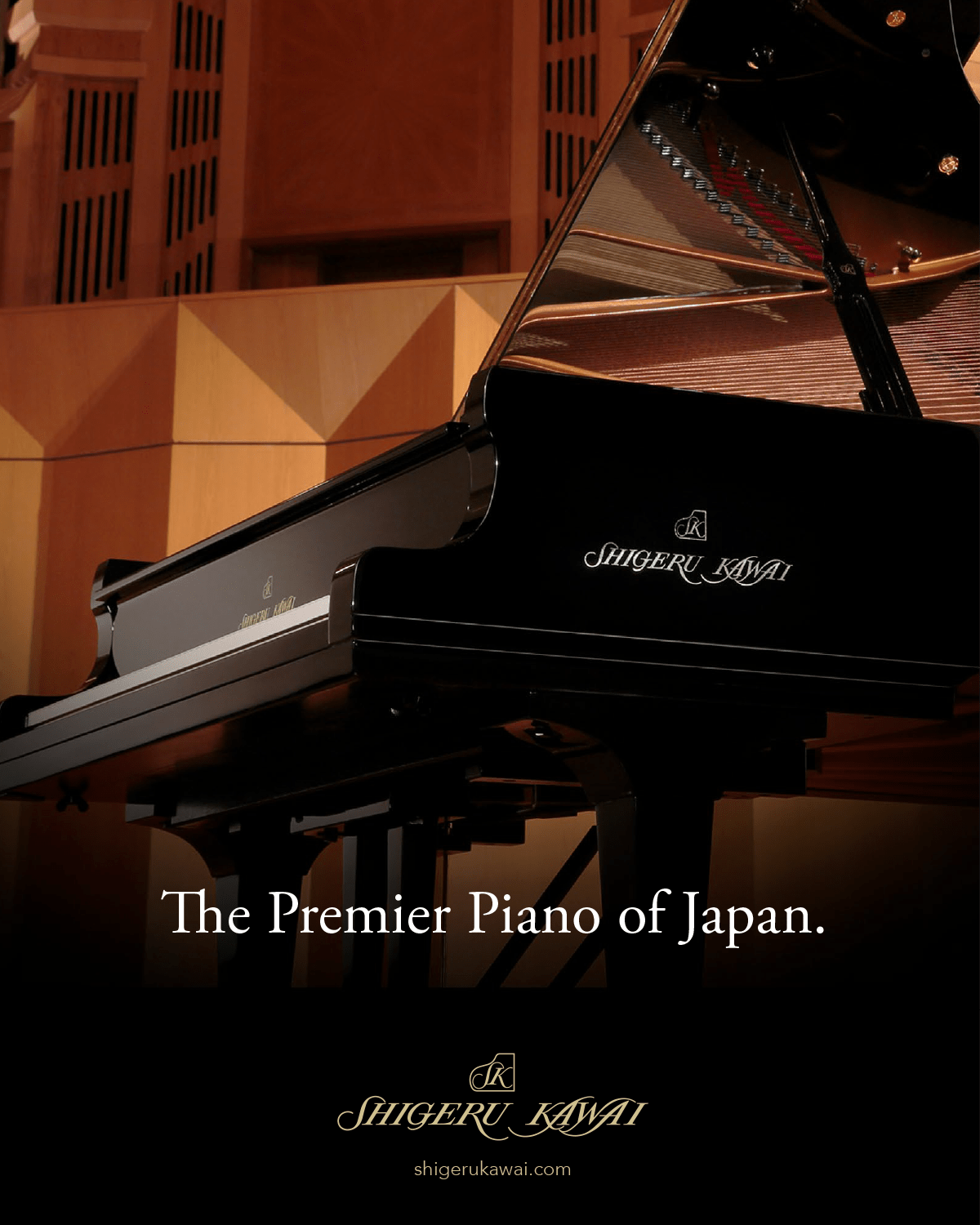
Design and Construction
In the interest of achieving better performance, appearance, or longevity, high-end piano makers are more likely to incorporate in their instruments unique or unusual construction methods or components, even though these may be more labor intensive and thus more expensive. Pianos that are more mass-produced, on the other hand, tend to include design compromises that enable faster or more efficient manufacturing. For example, the soundboards of most mass-produced pianos are shaped according to a design that is applied uniformly to every instrument of that model, whereas some high-end brands thin their soundboards by hand for best tonal quality, to compensate for slight variations in the wood.
Other examples of more expensive designs include unusual methods of bending or building up the rim, the use of multiple species of wood in rims or bridge caps, unique patented components for enhancing the tone, and more keys and/or strings than are found in a standard piano. Some of these design elements are present in part for reasons related to a brand’s history, others purely for reasons of quality, but each is there because it serves the performance objectives of the manufacturer and is part of what makes each brand unique. All such idiosyncratic variations add considerably to the time and cost of manufacture.
Settling-in Time
A very necessary but expensive part of building a piano is the time it takes the components to settle between stages of construction, and these periods will generally be longer in a factory making high-performance instruments. On any visit to a piano factory, one may be puzzled by the sight of many pianos and components sitting around in various states of completion, not being worked on. This seems counterintuitive to anyone from an industry in which the main measure of efficiency is getting as many products out the door in as short a time as possible.
But in piano manufacturing, patience is crucial to getting good results. Grand-piano rims may have to sit for months after being bent, in order to stabilize before they can be worked on further. In between action regulations, pounding machines are used to compress the action cloth. The pianos must be tuned numerous times to stretch the strings, with settling time between tunings. Hammers must be voiced to perfection by hand. In the long run, the time it takes to let the 12,000 or so parts of a piano get used to each other pays off handsomely in the form of greater longevity and stability of action, tuning, and tone.
Custom Musical Preparation
To maximize each instrument’s potential once basic construction has been completed, high-end pianos are given much greater musical preparation — tuning, action regulating, and voicing — in the factory. This highly skilled, exacting work requires years of training. Performing extensive musical prep at the factory ensures that by the time the piano reaches the customer, its tuning will be stable, and the cloth and felt used throughout the action will have settled; as a result, the piano will need less initial servicing by the customer. Because the skill and experience of the craftspeople in a high-end factory are almost certainly greater than what is available to dealers or customers, this also ensures that every step in the piano’s musical preparation has been performed, at least this first time, to a high standard, and that the instrument leaves the factory having fulfilled the manufacturer’s performance objectives. In my experience, a piano that has been stabilized in this manner will wear more evenly, have fewer and less idiosyncratic problems, and will be easier and thus less expensive to service throughout its working life.
Worker Training, Experience, and Autonomy
The craftspeople in companies that produce high-end pianos are highly trained, and because of the enormous investment made in that training, companies are willing to pay a lot to employ these people over many years. It can take years of experience, for instance, to become a skilled voicer. The better companies have extensive programs that gradually move employees into areas of greater responsibility, so that skilled replacements are readily available when needed. This greatly increases the cost of labor over companies that make less-costly instruments, where workers need not be so highly skilled.
In the making of high-performance instruments, more autonomy is given to individual craftspeople to make changes or corrections as needed. For example, in a high-end factory, a voicer unhappy with the tone from a particular set of hammers has permission to replace them. This is in contrast with high-production factories, in which workers may pay less attention to mistakes or unsatisfactory results, and flawed instruments may go far down the assembly line before being caught (if they’re caught at all), by which time making the correction may be too time consuming, and thus too expensive, to bother with.
Cabinet Detailing and Appearance
Between high-end and mass-produced pianos, there can be great differences in the quality of hardware (casters, hinges, pedals, screws), the thickness and surface preparation of the cabinet and plate finishes, the felt and cloth used in the case parts, and in the thickness and fit of the legs, lyre, and lid. Consumers may rarely notice these details, but they’re important to the instrument’s longevity, and affect the appearance and noiseless operation of all case parts.
• • •
Whether for a concert or for home, a professional pianist’s choice of high-end piano is primarily based on the instrument’s tone and touch: Does it sustain, to enable a singing line? Does it project the tone? Does it offer a wide range of dynamics and tonal color? Does the action repeat quickly and reliably, transfer power efficiently, and remain well within the player’s control? For the amateur pianist, high-end pianos open up a wider world of sound and performance than is otherwise achievable — and having that range of expression literally at one’s fingertips can lead to a tremendous joy in making music that is rarely experienced with lesser instruments.