With the conservative approach, the restorer places a high priority on preserving as much of the original instrument as possible, even, if necessary, sacrificing some degree of performance in the interest of maintaining historical authenticity (not just to save money). So with this approach, for example, rather than replace a cracked soundboard, a restorer would shim the cracks with wood (if possible, with old wood); and rather than discard and replace old wooden action parts, the restorer would replace only their worn leather and cloth surfaces. Design changes, even minor ones, are unthinkable.
With the modern approach, the restorer places a higher priority on the instrument's performance, and so replaces as many parts as possible with new ones. But the restorer attempts to make the piano only as good as it was when new, closely maintaining the original design. Sometimes minor design changes will be made to correct known defects, especially ones the manufacturer itself corrected in later instruments.
With the innovative approach, the restorer not only replaces worn parts with new, but also feels free to modify the design of the instrument in any way that, in the restorer's judgment, would make it perform better — even in ways the manufacturer never contemplated and might not approve of. So the thickness and taper of the soundboard might be changed, the bridges moved, the stringing scale altered, even new holes made in the cast-iron plate and pinblock to accommodate new strings — anything that can be done within the confines of the original case and plate is on the table for consideration.
In this article, several well-respected piano restorers, each approximately representing one of the above positions, explain their approaches to restoration in general and, specifically, how they might be applied to various eras of Steinway grands. — Editor
Conservation-Informed Piano Rebuilding
Bill Shull, RPT, M. Mus.
Twenty-two years ago, the purchase of an 1878 Style 2 (7' 2") Steinway grand piano led me down the road to a different approach to piano restoration. This piano was one of the last examples of antique piano building, and one of the last bridges to the modern era. It was a strange instrument, very unlike a modern Steinway and difficult to rebuild, and I learned that there were few existing protocols for restoring it. As a result, I was inspired to study these earlier Steinways—and earlier pianos from other makers—more thoroughly, and sought to learn more about the field of conservation in general. Since then, my research and teaching have brought me in contact with leading conservators and their work, and in my presentations and classes I have begun to encourage my colleagues to be more careful in modifying older pianos, and to become familiar enough with conservation to give responsible counsel when retained to assess and appraise older instruments.
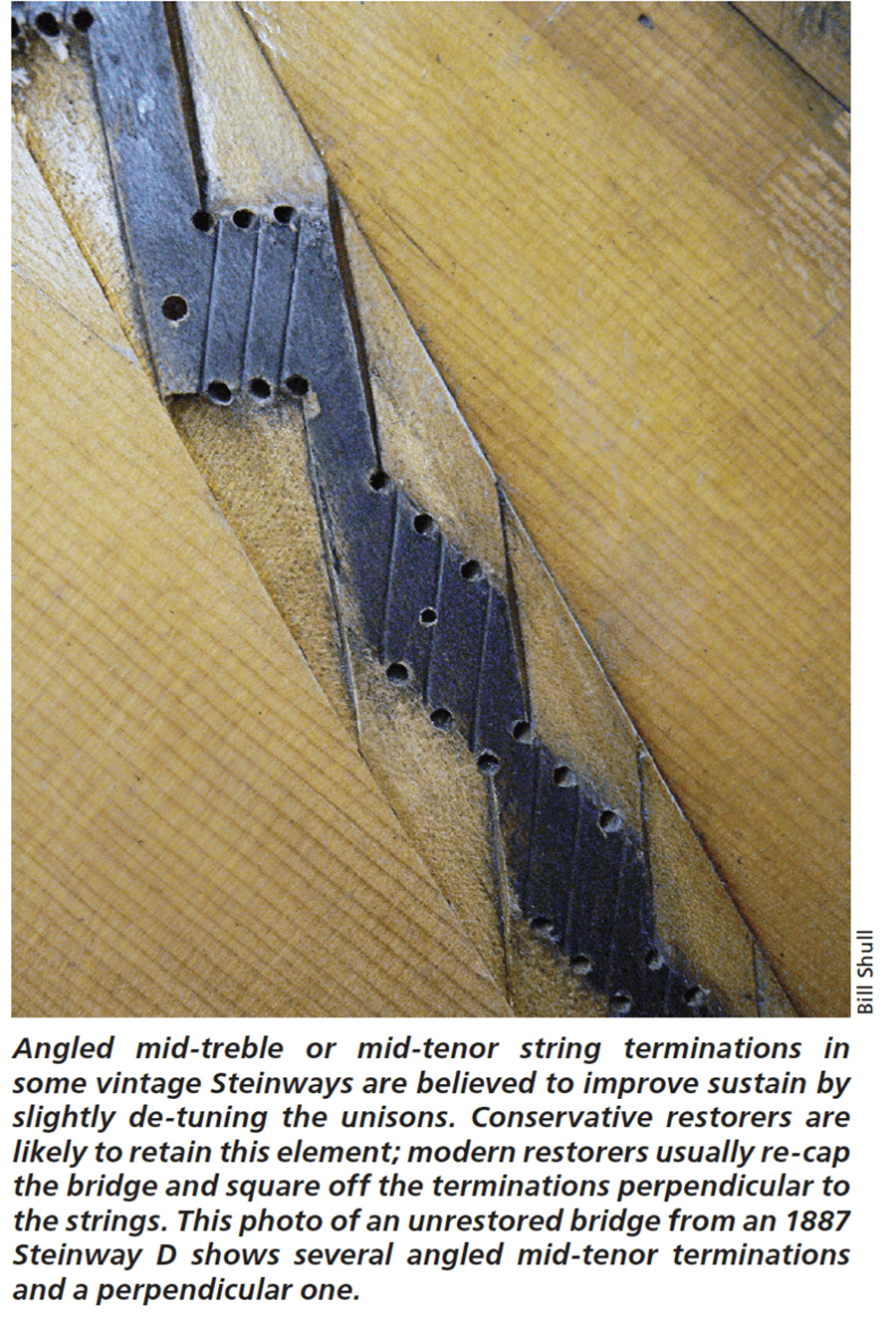
What has cemented these convictions has been my experience in locating early Steinway pianos for my study. As I examined rebuilt examples of early Steinways, I found, among rebuilders, a widespread disregard for these pianos as objects of conservation, and nearly equal disregard for restoring them to their original structural, mechanical, or musical design. Permanent alterations routinely include replacement of soundboards, bridge caps, and action parts, and the use of near-permanent polyester or polyurethane finishes. Some alterations include experimental designs. If the piano is antique or historically important—things not always easy to know—its historical value, and probable future value as an antique piano, can be lost forever in the rebuilding shop.
This lack of respect for early Steinways can be shown even by conservators and early-piano specialists, who may recognize the emergence of modern design elements but can have insufficient regard for these instruments as historical documents. Steinways from 1853 to 1892 represent an era of transition: from flat-strung to cross-strung; and from antique soundboards with long cutoff bars and grain parallel to the spine, to the modern crowned soundboard supported by angled ribs and grain. Before 1860, pianos were, to a great extent, built by hand, but by 1880, construction techniques had been mechanized and standardized. So while early Steinways tend to be ignored by students of the early piano, these instruments are critical to an understanding of piano history, and deserve respect as objects of conservation. Even “modern” Steinways from the 1880s to as late as the 1930s can contain design nuances that are often glossed over and discarded by the modern rebuilder.
This attitude follows the lead of Steinway & Sons’ own Restoration Center, which usually treats antique Steinways like their modern counterparts, and in restoring them seems to follow no consistent policy of conservation. There is a certain irony to Steinway’s relative lack of interest in its own early instruments, for the stories these pianos tell are of some of the company’s best, most enduring innovations. Indeed, it was the antique, 1860s design of my Style 2 Steinway that catapulted the company to industry leader in 1867!
While it is generally thought, among piano restorers, that conservation is for only museum objects, consumers increasingly seek competence in restoring antiques from professional piano restorers. Not only is the general public becoming more aware of the value of conserving antiques, but pianists are increasingly interested in performing music on instruments from the period in which the music was composed. This development in piano performance practice relies on the availability of well-restored original instruments and good replicas.
Leading conservators, curators, and early-piano experts have had a profound influence on my rebuilding and have helped me to define my work. Especially important has been Robert Barclay’s seminal book, The Preservation and Use of Historic Musical Instruments: Display Case and Concert Hall (Earthscan from Routledge, 2005). Barclay explains that, among the options for conservators of musical instruments, none satisfactorily permits both continued use (“currency”) and historical preservation (“conservation”), and the “restoration” option invasively alters the historical document. Barclay defines a mediating alternative that he calls “restorative conservation”: careful application of conservation principles and techniques in a manner that permits those who wish to play and hear the instrument to do so. It is this philosophy of restorative conservation that I attempt to follow in my shop.
Applying restorative conservation to piano rebuilding requires making many difficult and nuanced decisions. A few examples:
Bridge modification or careful wire selection. Modern rebuilders solve wire-matching problems by adding wound strings, or by moving or adding bridges. For example, the top two octaves of early Steinways had shorter string lengths and more flexible music wire than modern Steinways. Today’s stiffer wire requires longer strings, so rebuilders often move the treble bridge to increase the effective string length. However, to maintain the historical integrity of the original instrument, I no longer move the bridge, but instead seek out the best available replacement music wire intended for period instruments, several types of which have recently become available. I also document the original scale and archive the old music wire.
Early damper actions. Early Steinway damper actions used a damper wire that threaded into the wooden damper-lever flange, or a setscrew threaded into wood. These systems did not age well, and sometimes cannot be successfully restored. Since most Steinways can be retrofitted with a complete, new damper action without any compromise of design, I often take advantage of that alternative, saving the original parts (or representative samples) for future study. Options also exist for partial replacement of the damper action where that would suffice.
Bass strings. Even with modern restoration techniques, old iron-wound bass strings rarely approach the tonal palette of properly designed new ones. If the owner wants to return the instrument to its highest possible performance level, the original strings will be replaced and saved for future study. Depending on the owner’s use and preference, for greater authenticity, I may replace old iron-wound strings with new ones of the same material, or, for greater longevity, with modern copper-wound strings.
Hammers. It’s a cause for celebration when I find a completely original piano, including the hammers. (The hammers and finish are usually the first things to be replaced, followed by the strings.) No solution for hammer replacement satisfies everyone. Technicians will usually reshape the hammers to eliminate the grooves. Conservators prefer to send the original hammers to Europe to have their wooden moldings recovered with new felt, retaining as much as possible the weight and resilience of the originals; however, this still destroys the original hammer as a historical document. I prefer to replace the entire action so that the original action can be saved intact for historical study. More often than not, however, the client cannot afford this, in which case I prefer to replace the hammers with new ones of similar weight and density, along with the shanks and flanges, and save the originals for the historical record.
Steinways built between 1864 and 1880 usually have actions that appear modern, but have a much higher action ratio (leverage). These are cumbersome to play with the heavier hammers of the modern era, including modern New York Steinway hammers, so I encourage the use of lighter hammers and higher gearing on Steinways (and other makes) originally designed that way. I also retain original rocker-style capstans instead of retrofitting with new screw capstans and new-style wippens.
Soundboard and bridge caps. The soundboards of most pianos built through the 1860s last far longer than is commonly believed, because they are not of the “crowned and loaded” design of the modern piano, in which the stress applied to the soundboard tends to shorten its useful life. Even the more modern crowned soundboards may still be viable, as the modern soundboard design always has a significant functional stiffness, even if there is no crown. If I must replace the soundboard, I copy the original design, extensively document my findings, and retain the original soundboard as an artifact. I also prefer to retain any unique design elements, such as the angled mid-treble unison terminations used on Steinway Cs and Ds from 1884 through the 1930s, and faithfully replicate them if a bridge must be recapped. This unusual element adds sustain and projection power to the treble by slightly de-tuning the unisons. Squaring the termination to tame the resulting slight false-beating “wildness” of sound neutralizes the designer’s intent for the treble tone (see illustration).
The Steinway piano has dominated the field of piano restoration, resulting in the mass disposal of many other venerable brands of high quality. Surviving examples of these other brands, however, are often in near-original condition. I’m especially joyful to find pianos in this state of benign neglect, as they represent a variety of tonal and performance ideas that could still have a voice through responsible, conservation-informed rebuilding: the articulate, Érard-like sound of the 19th-century Weber; the warm sustain of the three-bridge Knabe; the distinctive registrations of the flat-strung Chickering; the easy touch of the Edwin Brown action often found in Chickerings and other makes; and the sweet, warm sound of the Viennese piano.
Today, when restoring pianos, most rebuilders routinely replace parts, and many extensively redesign the instruments. While these approaches have their place in the piano rebuilder’s repertoire, indiscriminately applying them to vintage or antique instruments risks changing the unique historical, tonal, and performance character of the restored piano. Our rebuilding shop seeks to reveal the unique musical personalities of historical instruments while respecting their function as historical documents. It is not always possible to do both, and we are always leaning one way or the other, but it’s a fascinating and rewarding journey.
A Modern Approach to Piano Restoration
David G. Hughes, RPT
In the undertaking of any task, prudence dictates establishing a list of goals and standards, and the art of piano restoration is no exception. I take a modern approach to piano rebuilding. I grant myself liberty to make those mechanical and structural changes that result in lengthening the instrument’s working life, and in restoring the classic tone and touch it once possessed, but no more: in my shop, a vintage Steinway remains a Steinway.
I like to divide a piano and its rebuilding into three main areas of concern: the vibrating system or belly, the action, and the case. Three qualities must be present in the belly: immediacy of sound, projection, and sustain (the harmonic content and brightness of the tone are refined later in the process, when the hammers are installed and voiced). The belly should possess an abundance of horsepower—controlling an excess of sound is preferable to grasping for something that isn’t there. The keyboard and action should be capable of any demand. The touchweight should be 54 grams at the lowest note, tapering off to 47 grams in the top octave; the speed of repetition should be such that no performer can outplay it; and player fatigue must never be an issue. The rim and its associated structural components must be rock solid, the cosmetic veneer and case parts absent of defect, and the reapplied finish showroom-new in appearance.
In the belly, my approach is to build everything new within the capability of a small shop. This means the rim and plate are retained, and everything else discarded. Specifically, the ribs, soundboard panel, bridge caps, trim moldings, pinblock, tuning pins, and strings are replaced. As well, the plate receives a gleaming new finish with hand lettering, nickel-plated hardware, and new agraffes, hitch pins, and felts. I always retain Steinway’s original string scale. However, I modernize the skewed treble-bridge notching of older models B, C, and D with modern perpendicular terminations, as Steinway does in its own factory restorations.
I honor the piano’s original rib locations and lengths. I have created my own ideal rib depths (thicknesses) for all the Steinway and Mason & Hamlin models, loosely resembling the original dimensions—which, in any case, varied slightly from instrument to instrument, even of the same model. Where I part ways with tradition is in how I crown the soundboard. Unlike Steinway’s compression crowning, in which straight ribs are forced into a curved shape by bending them during the crowning process, I choose to cut the curved shape into the ribs by machining them. A compression-crowned soundboard is indeed lively at first, but, in my experience, can prematurely lose its aural luster. In my approach, the ribs are cut to the intended radius of crown, then glued to the back of the soundboard. Done this way, there is virtually no stress at the rib-to-panel glue joint, and the cross-grain pressure on the soundboard (so-called compression crushing) is greatly reduced, virtually eliminating the possibility of damage to wood fibers. When the soundboard is judiciously loaded with the string plane’s downbearing, decades of musical sparkle will result. Improved tuning stability is a fringe benefit, as this stiffer soundboard is not as easily influenced by swings in humidity.
So what should all this techno-talk mean to the discerning rebuilding client? Of the three desirable belly attributes cited earlier, immediacy and projection are instantly appreciated when heard, if difficult to quantify. Sustain, however, is easily expressed: A mezzo forte blow on D in the fifth octave should linger nicely for at least 12 seconds without enhancement by the sustain pedal. Melody-range notes one octave higher should sustain about two-thirds as long. A seven-finger fortissimo chord spread across several octaves while employing the sustain pedal should dwell considerably longer than is musically necessary.
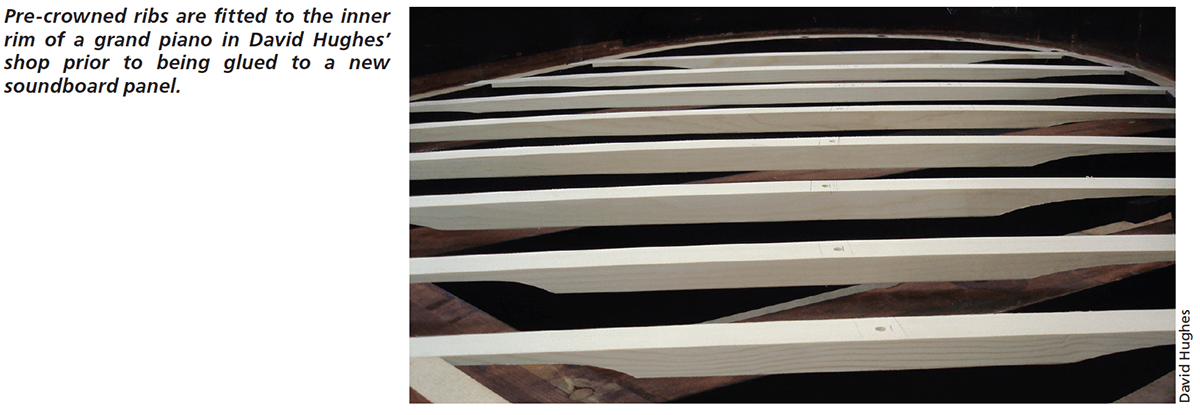
The only original elements of the keys and action I retain and restore are the keyframe, tubular metallic action frame, and damper heads. Eighty-eight new keylevers are designed and fit to the rebuilt keyframe, with top priority given to convergence (the interaction of the moving parts in a manner that minimizes friction) and optimal action leverage ratio (ratio of hammer movement to key travel). When the vintage (pre–World War II) Steinways were built, these critical requirements fell prey to small variations in plate location that occurred while fitting the pinblock. This defect can be rectified by a custom rebuilder. The keyframe is fitted with anodized-aluminum keypins that are virtually frictionless, and the keys receive capstans of the same material.
The action frame receives a fresh gold-colored finish, new letoff screws and buttons, hammershanks, wippens, and hammers. I insist on using Steinway hammers in Steinway pianos; I have found them essential to achieving the classic Steinway tone. A raw set of hammers from Steinway’s Parts Department requires nearly two days of prep work in my shop to achieve the ideal shape and weight. Final voicing efforts are equally meticulous.
I endorse Steinway’s Accelerated Action concept, placing the lead required to counterbalance the weight of the hammer action as close as possible to the balance point of the key. One cannot argue with the physics of inertia and momentum: If lead is installed near the front end of the key, angular momentum is increased and repetition is rendered substandard. The closer to the balance point this weight is located, the less it is noticed by the player.
With the keyboard and action complete, I install a new damper tray and damper underlevers. However, unlike Steinway’s procedure, I locate the pivot point for the tray in line with that of the underlevers, resulting in identical performance and regulation for both key lift and sustain-pedal engagement. To minimize noise and friction, I also modernize the vintage-style connection between the sustain-pedal trap lever and the damper tray, as Steinway has recently begun to do. Further, I install lift capstans for the underlevers on the damper tray to perfect the uniformity of damper engagement by the pedal, a result not truly attainable with Steinway’s factory setup. The damper heads receive a fresh ebony finish and new damper felts, and the damper guide rail is rebushed to guarantee snug damping. After assembly and initial adjustment of all parts, the keyboard and action spend eight hours on a pounding machine to settle the regulation and voicing.
Old pedal lyres typically come unglued vertically. As the discovery of a spreading pedal lyre three months after a restored piano is delivered to the client is no joyful revelation, during the restoration process I routinely coax apart all glue joints and renew the entire structure. The pedals receive new bushings and felts, as does the trapwork on the underside of the keybed. With all due respect, Steinway’s system of limiting the throw of all three pedals is archaic. I install heavy-duty, infinitely adjustable stop mechanisms in the trap levers to introduce precision and ease of regulation for decades to come. Finally, I repaint the undercarriage the original factory color so that the instrument appears completely new from any angle as it is rolled into the customer’s home.
The instrument’s case receives a hand-rubbed, closed-pore, satin finish. New furniture parts are fitted and applied as necessary, with particular attention paid to the lid and legs, which tend to split with age. All of the piano’s hardware is either replated in nickel or polished in brass, as appropriate.
With this recipe complete, only the instrument’s reapplied serial number reveals its age.
Value-Added Rebuilding
Delwin D. Fandrich, RPT
Over the past 35 years, I have developed the concept of redesigning pianos while rebuilding them because the results of conventional restoration and/or rebuilding were no longer satisfying. For lack of a better term, I call this concept “value-added” rebuilding.
Assuming competent work, conventional rebuilding—i.e., replicating and restoring the instrument’s original design and construction—will return a piano’s performance to its original level, but that will include the original design’s weaknesses as well as its strengths. Though I began as a conventional rebuilder, increasingly those weaknesses bothered me. I began searching for ways to keep the best parts of each piano’s intrinsic voice—its natural timbral character—while improving or eliminating weaknesses in its original design.
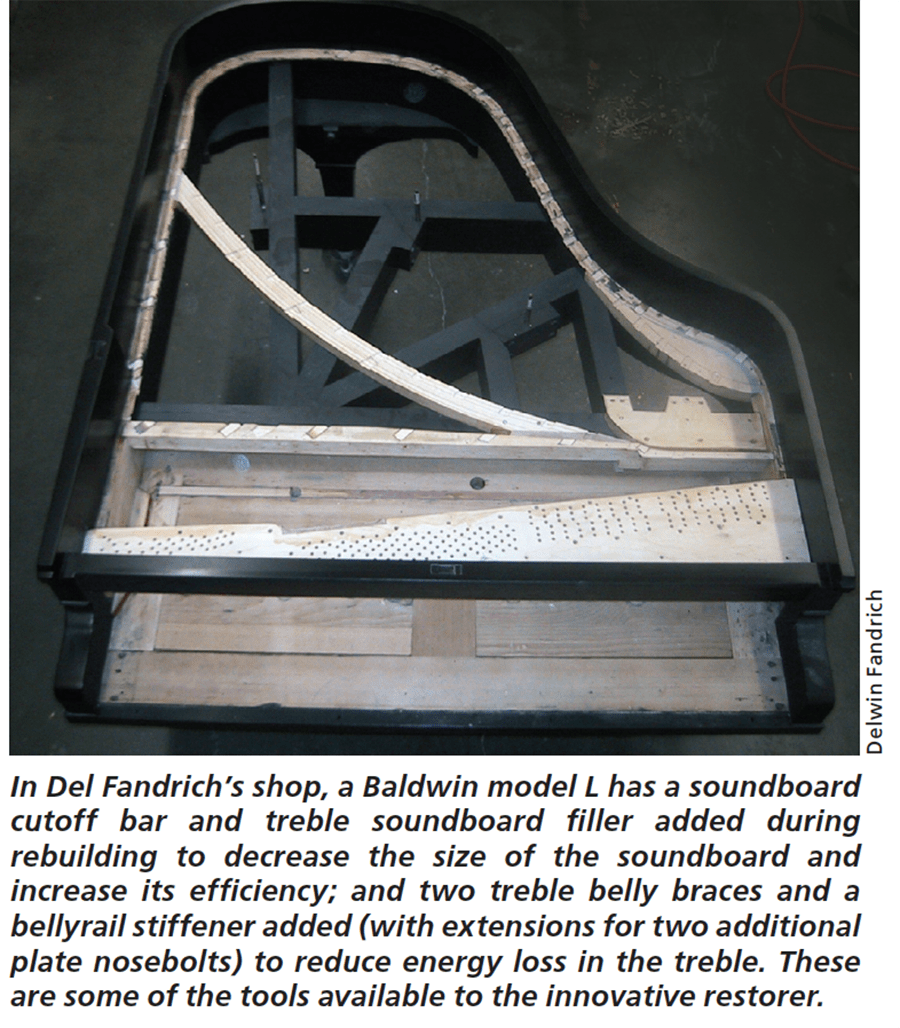
For the value-added rebuilder, the piano’s brand name and year of manufacture are not important considerations. It is important that the original instrument be structurally well made, but many brands with essentially similar designs and construction provide the value-added rebuilder with equal potential. For example, a 1970s Kimball 5' 8" grand—not usually well regarded—shares enough core design and construction details with the Steinway Model M grand that, for the value-added rebuilder, its potential is essentially the same. Major components of the original—such as the stringing scale, the soundboard and rib set, and the bridges—are going to be redesigned and replaced anyway. At the end of the process I would expect the same level of performance from both, with the design weaknesses of both pianos being improved, and the tonal qualities of the Kimball becoming much more like those of the Steinway.
By subtly changing the design, it becomes possible to tailor a piano’s performance more closely to the owner’s personal preferences. With my own pianos, I can suit my personal taste. I want the overall warmth and dynamics of the wonderful American pianos of the early 20th century without their common weaknesses—an indistinct lower bass, uneven bass/tenor break, and choppy or percussive tone in the upper tenor and low treble. With appropriate redesign, I can achieve a clear and distinct bass, a musically transparent bass-to-tenor transition, and a clear and sustaining voice through the upper tenor and low treble. I can have a common timbre across the compass of the scale—a piano that sounds “all of a piece,” with a unifying tonal quality throughout all sections.
Because the basis for the overall timbre, or tone character, of any piano is its stringing scale, that is where I start. Both the relative lengths and tensions of the original scale are considered, in an examination that reveals the range of tonal options I have with any given piano. A piano originally designed with a low-tension scale will be limited to a low-tension scale. For example, the smaller Steinways have scales that are relatively low-tensioned but erratic; to raise the string tensions on these instruments is structurally and tonally unwise. The beauty of these pianos is the warm, dynamic sound characteristic of low-tensioned scaling. I will give them a more balanced and consistent tone across the keyboard, and improve the quality of voice in the low bass, but their basic character will remain.
A piano originally built with a high-tension scale, such as a larger concert grand, presents a wider range of options. For example, because many pianists love the clarity and extended sustain characteristic of the concert grand’s low bass, more of these instruments are now being found in private homes. But the percussive power of the concert grand is so overwhelming in a small space that it can mask a great deal of musical subtlety. With appropriate redesign, the acoustical palette can be matched to the smaller space. The bass retains that wonderful, long-string clarity and sustain, but the whole instrument becomes more balanced and controllable.
Another option with redesign is to adapt the tonal palette to better suit a particular musical style. Many pianists find the percussive power of even the more lightly-strung modern pianos inappropriate for works by the early classical composers. For these players, the piano’s design can be altered to give a more subtle and delicate voice, to emulate the sound of the pianoforte of the mid-19th century. The action can be given a lighter, quicker touch and feel, while retaining the reliability and consistency of a modern action.
Achieving acoustical balance is a common goal of the value-added rebuilder. Most of the stringing scales found on vintage pianos—and more than a few new ones—are very uneven. New stringing scales that meet the new acoustical goals set for the instrument are designed, and new bridges are built to suit. Particular care is taken to blend the piano’s voice across the bass-to-tenor transition; by its nature this transition should be imperceptible to the musician and should not require extensive hammer voicing to mask any inherent shortcomings of the fundamental design. In recent years, low-tensile–strength music wire has become available. This wire is more flexible than traditional music wire. Its selective use in certain parts of the scale—a technique called hybrid scaling—can make achieving a musically transparent bass-to-tenor transition much easier.
It’s critical that the vibrating characteristics of the soundboard match the character of the stringing scale. Until the 1970s, the design and function of the modern piano’s soundboard was shrouded in mythology. Since then, the hundreds of hours and thousands of dollars invested by many rebuilders in study and experimental work have given them a whole new set of design tools to work with that allow them to accurately predict the acoustical performance of a new soundboard design. The effects of soundboard thickness, grain orientation, and ribs are better understood, so rather than simply duplicating the original soundboard—which may or may not have worked all that well—new soundboards can now be designed and built to work predictably in synergy with the stringing scale. Ribs are usually crowned to a precise radius, and are cut to a calculated thickness and height to carry a known string-downbearing load. Rib locations can be moved to better distribute the vibrating energy of the strings, and to control unwanted resonances and give the piano a smoother voice. Soundboard shaping devices such as cutoff bars are used to reduce the size of the soundboard and make the system more efficient.
Today’s rebuilder also has a wide selection of actions from which to choose. These range from simply replacing the wippens and hammershanks with new wood components from Renner or Tokiwa, to fitting a completely new composite action stack made by Wessel, Nickel & Gross. The range of options for tailoring action characteristics to suit the individual performer has never been greater.
With the proper balance between the stringing scale and the soundboard system, hammer selection becomes relatively easy. The value-added rebuilder will have a good understanding of the physical characteristics of the aftermarket hammers available—and today the choices are excellent—and will know which hammers will best suit the particular piano he or she is working on. Ideally, the hammers will require a minimal amount of voicing. Indeed, excessive hammer voicing is always an indication that something is out of balance: either the stringing scale and the soundboard system are not well matched, or the wrong replacement hammers have been selected.
Rebuilding a piano in this fashion costs very little more than conventional rebuilding, and supplies the pianist, amateur or professional, with an instrument specifically tailored to his or her personal taste, and that will provide a supremely satisfying musical experience.