The Rising Quality of Mid-Range Pianos Is Crowding Out the High End
by George F. Emerson
Between the emergence and the decline of an industry come the more productive phases of growth and maturity, and to the extent that a company is willing to invest in adapting new technologies to its particular product, that company may move out of maturity into a new growth phase. The piano industry, however, seems to be an exception. To accurately describe the piano industry, we need to inject another phase between maturity and decline: for want of a better term, the geriatric phase. Few consumer-product companies can survive without making continuous efforts to expand the capabilities of their products — Ford wouldn't have lasted long had it remained content with the Model T — but such stagnation often afflicts mature piano companies.
One important reason for this is that the piano repertoire spans centuries, and is just as vital and timeless today as when the music was first composed. This is not to say that the styles and standards of musical performance do not continue to grow and develop; they do. But the music of the old masters is just as viable today as are newer trends in music, and as welcome on the same stages of musical performance. By contrast, the programs written for the earliest personal computers are now hopelessly obsolete in comparison to the current family of computer software.
While a piano manufacturer might rely on the timeless nature of music to extend the viability of its product for decades longer than would be possible in other industries, a geriatric status is not a healthy place to be. The piano manufacturer willing to innovate stands a better chance of sustained growth over a longer period.
_______________________________________
As an example of the tradition-bound nature of the piano industry, at a time when computer-aided design (CAD) software was already commonplace in other industries, an engineer at the Baldwin piano factories of the 1990s was not taken seriously if his desk did not display a slide rule. The most prominent feature in his office was a drafting table, modified with a large-enough top for the full-scale layout of a 9' concert grand. He would not venture onto the factory floor without packing a vernier caliper in a holster. At a time when every do-it-yourself handyman had at least one electric drill at his disposal, Baldwin factory workers were still using Yankee screwdrivers. (The reader might remember his or her grandfather using such a tool. When the handle is pressed in the direction of the screw, the shaft telescopes into the handle with a spiraling motion, giving the screw a few turns. Replace the tip with a straight-flute drill bit and it serves as a drill for the pilot hole of the next screw.) Even in a Chinese piano factory, an accountant was observed to prefer to crunch numbers with an abacus that sat next to his desktop PC. All of these are examples of the piano industry having been behind the times in most technological development.
Why was Baldwin still content to use Yankee screwdrivers when better tools were available? Because such tools were part of the company's culture; it was tradition. When a company's success is still based on a product they were building a century ago, it's hard to justify doing things differently. This resistance to change is a strong indicator that a company is in the geriatric phase of its life cycle. In most industries, a company will go into decline before it gets bogged down in this stifling aspect of company "culture." In the piano industry, due to the timeless nature of the piano repertoire, and the supposed timeless nature of the instrument itself, this geriatric phase can endure for decades, while the company's strength atrophies.
Even when a piano manufacturer finally comes around to using a new technology, it is often not applied in a way that would use that technology to its best advantage. In the early days of computer numerically controlled (CNC) machining, the human interface with the machines was very poor, and computer programs for generating the control codes were nonexistent. To enter codes in some early CNC machines, the engineer would print out hundreds of lines of code, then enter each digit of code, one at a time, via a handheld data-entry device.
In the 1980s, when engineers at Wurlitzer decided to use what would probably be called a precursor to today's CNC machinery to manufacture keyboards, they faced a dilemma. To accommodate the unique string and hammer spacing of each model, which requires that the keys for each model be of slightly different shape, they would have to program the machines multiple times. Rather than do the hard work of writing new code for each model, Wurlitzer's engineers took an easier path: They standardized the shape of the front half of the key, where all the complicated cutting was, by making it perfectly straight from front rail to balance rail, then concentrated all of the required differences in shape into the short space between the balance rail and hammer. To achieve this, the angle at that point in the key had to be extremely sharp. Many readers will remember the resulting so-called "dogleg" keys. The grain angle at the bend was such that the keys were extremely susceptible to breaking, and the torsional force on the balance point of each key was so lopsided and extreme that the key bushings on one side would wear out virtually overnight. Computer-controlled machining lowered the cost of manufacture, but instead of improving the quality of the product — one of the technology's supposed benefits — the quality was actually reduced.
Despite this sort of false start in the application of new technologies, there were other instances in which a new technology had almost magical results. The very foundation of the piano is its cast-iron plate. A multitude of earlier piano-manufacturing production problems had a common cause: the unpredictable dimensional distortion that occurs when such a large iron casting cools and solidifies after being poured. CNC milling made it possible to correct these inconsistencies — and getting all of the plate's critical dimensions right positively affects just about every operation that follows.
But there were some false starts in the CNC machining of plates as well. A critical concern was to precisely control the bore depth for each agraffe — the device that terminates the speaking lengths of the strings at the tuning-pin end, and also serves to control the note spacing, string spacing, and string height. Even the earliest CNC machines were precise enough to fulfill this important objective. Unfortunately, the machine's precision can be defeated if the plate is not properly supported on the milling table. In the early days of CNC plate machining at O. S. Kelly, the only U.S. manufacturer of piano plates, one could see the plate being deflected ⅛" to ¼" under the downward thrust of the machine tool. You can be sure that the hole was not drilled to the precise depth required. This and other problems had to be worked out before the piano industry could realize the full potential of CNC machining.
Newer technologies have also led to design improvements. Slow-motion photography has advanced our understanding of what actually happens in the dynamic motion of the piano action, leading to improvements in action performance. Computer-simulated motion studies have made it possible to predict with great accuracy the movements of action and soundboard even before the first physical prototype is built. Finite Element Analysis (FEA) measures, in cyberspace, the deformation of parts under the impact of controlled forces. This is not only useful in analyzing the action, but also in designing the ribs, to provide adequate support to the soundboard throughout the scale. Electronic equipment can visualize sound in a fast Fourier transform (FFT), which breaks down sound into the relative strengths of its harmonic partials. These sorts of tools can verify what we think we know and/or hear, or teach us otherwise. No doubt we have not yet arrived at the best a piano can be, and with the application of yet unknown technologies, we'll continue to make improvements.
Many modern piano factories produce dozens of brand names, from cheap to expensive. With such a wide range of quality being built under one roof, it's inevitable that the manufacturer will learn from the high end of their production what can be applied to the low end at little or no cost, to raise the latter's quality level. These technological advantages have also made it possible for new, up-and-coming companies to design and build an excellent product in an extraordinarily short development time, and to a higher level of quality at a lower price.
Nevertheless, there are still those who believe that "they don't make ‘em like they used to," and who would further assert that the best piano available today is a century old, and has been restored in a way that remains true to its original design with "genuine" parts. Others would argue that if such an excellent instrument has been built before, it can be built again, and just as well. Furthermore, with the application of new technologies, it can be built with even better quality, with a greater degree of consistency, and at a lower cost due to greater efficiency. They don't make 'em like they used to? Quite true. For the most part, we now build them much better than we used to.
"Hand-built" used to be the hallmark of a quality piano. Many high-end piano builders trumpet "hand-built" as justification for their higher prices. But in today's reality, "hand-built" does not automatically equal higher quality. It harks back to a time when uncontrollable inconsistencies required higher levels of skill to work out Band-Aid fixes to overcome those deficiencies.
In the Golden Age of American piano manufacturing, in the early 20th century, true talent was required of master piano builders. It was essential that those highly skilled craftsmen be able to take a flawed cast-iron plate and make it work when parts didn't quite line up, and when the strike point at the string was not at precisely the correct height from note to note. When we finally made use of the precision and repeatability of CNC milling of the plate, virtually everything else in the production process fell into place. Less time is now expended working around unpredictable deviations. We can build a better-quality piano at lower cost, with less reworking to fix problems that no longer exist. With the proper application of modern technologies, a well-designed piano still requires skilled workers, but their skills can now be focused on precision and consistency, not on perpetual problem solving.
Most Americans are saddened by the loss of jobs and entire industries to China, but there is a positive side to this circumstance. China's new and growing piano-manufacturing industry is just emerging. Unencumbered by tradition, these manufacturers are eager to apply the newest technologies. They are fully implementing all of the promises of each new technology, reducing costs, improving consistency, and raising quality to a higher level than could otherwise be attained. True, the early Chinese pianos were poorly designed and built. But anyone who would loudly complain about the poor quality of early Chinese pianos should take a serious look at some of the poorly designed and built American pianos of the mid- to late 20th century. Many of those self-destructing piano-shaped objects don't measure up to the quality produced by many companies in China today.
Some companies, determined to produce the very cheapest pianos, will use new technologies to the extent that they reduce cost, even if it is at the expense of quality. At the opposite extreme, many of the makers of high-end pianos continue their "handmade" mantra. However, the piano makers in the middle, who use technology to improve quality first, and see cost savings as a secondary benefit, are the real beneficiaries of technology. While there will always be those who believe that the most expensive must be the best, moderately priced pianos are now challenging those at the high end.
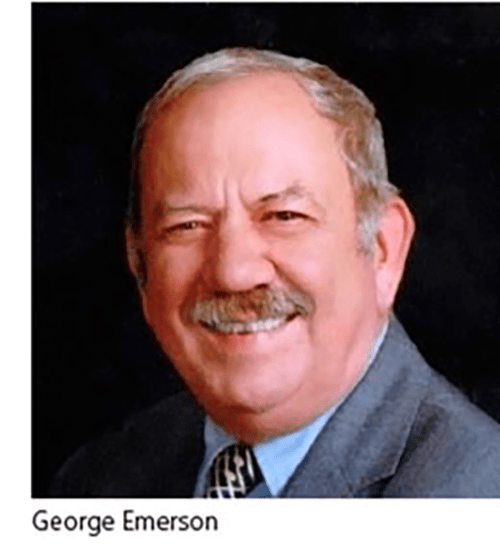
George F. (Frank) Emerson has been working in the piano industry for 48 years, including 11 years as a university technician and 23 years designing pianos for manufacturers, including Baldwin, Mason & Hamlin, and Hailun. He has been a Registered Piano Technician (RPT) member of the Piano Technicians Guild for 38 years. Emerson currently consults part-time for Hailun. He can be reached at pianoguru@cox.net.
"Hand-Built" Not Going Out of Style Anytime Soon
by Don Mannino, MPA, RPT
As a company that arguably makes the widest range of pianos in the industry today, from low-cost console pianos for the home (with many thousands built each year) to very expensive and limited-production concert grands for the stage (only about 12 per year), we at Kawai are perhaps uniquely qualified to speak of the different processes used to make pianos, and the results they make in the final product.
The important factor to remember is that, along with processes and machines, all pianos are made by people. The very high skills of the most knowledgeable and experienced craftspeople, applied to the construction of an artist-level piano — that is, what might be called "handcraftsmanship" — definitely lift the instrument to a higher level than can be achieved using normal production methods. This is borne out by the testimony of both experienced piano tradespeople and, perhaps more important, by pianists themselves when comparing similar pianos made using different processes. Pianists sampling well-prepared examples of Kawai RX and Shigeru pianos will almost universally acclaim the superior tone and touch of the handcrafted pianos, even though the designs are very similar.
Shigeru Kawai has found a unique way to incorporate the benefits of both styles of production into our pianos. It is possible to use extremely precise CNC machine processes in some areas of the piano where they are beneficial to the instrument, such as plate casting and machining, accurate indexing systems for consistency when assembling major sections of the piano, and manufacturing the small parts of the action, which benefit from extreme precision in all of our pianos. But for the finest pianos, some processes will result in a better instrument by being carried out in a slower, more traditional method by the most highly skilled artisans. A blending of both traditional hand work and precision CNC production has proven extremely successful for Kawai. The balancing of these processes, plus the selection and handling of the raw materials, combine to create the musical instrument that our customers desire.
Let me illustrate by providing an example. Hammer felt is ordered from the felt maker with very precise specifications for fiber type, thickness, and density. Yet when it has been cut and pressed into a set of hammers using very accurate CNC machinery, two sets of hammers made from the same sheet of wool can sound different. When comparing hammers made from one sheet of wool with those made from another sheet, there is even more potential for tonal differences, even though the specifications are verified and measure exactly the same. One could argue that the specifications are not precise enough, but the "resolution" of our measurements simply cannot take into account how the wool fibers will stretch and pull against each other in the hammer press, changing the tone of the hammers. Pressing them with high heat and extremely consistent machinery helps make them more consistent and predictable, and most higher-volume piano makers use hammers made in this way — but this type of hammer does not have the potential for as wide a range of tone colors as hammers made with the slower, hand-pressed method.
In the end, the best way to control the tone is for experienced people to make the hammers, and for experienced people to adjust the density and shape of the felt by voicing the hammers at the end of the production process. For the Shigeru hammers, years of testing and experimentation in our Research and Development laboratory taught us that a hand-operated hammer press worked by an experienced craftsperson allows the pressure to be fine-tuned according to the feel of the wool in the press. In addition, pressing the hammers with very low heat affects the resilience of the felt and makes it possible to voice the hammers with a wider range of tone. The Shigeru Kawai hammers require at least six hours in the press, as opposed to 15 minutes for many production hammers. This "cold press" process would be too expensive, requiring many highly skilled workers and many more hours of labor, for high-volume-production pianos. But for limited-production, higher-priced instruments it is possible to spend this extra time, and the buyers of this level of piano will appreciate the range of sound and tonal control provided.
Many other examples can be listed of differences in high-end pianos that make them more expensive and more refined as musical instruments: long-term natural seasoning of soundboard wood; hand-planing of soundboard panels according to the stiffness of each piece of wood, instead of simply trimming it to a specification; sorting or hand-trimming the 88 hammer shanks in a set for the best tone; hand-spinning the copper onto bass strings, to give a fuller sound than possible with CNC-controlled tightness. These processes and many others come together to elevate the musical quality, the touch and tone, of a fine piano to a higher level than can be created when piano production is focused on consistency and efficiency first.
All pianos are, to varying degrees, built using both machinery and hand processes. A piano becomes a "handcrafted" instrument when the skill of the craftspeople building the piano contributes more to the musicality of the finished instrument than does the precision of the tools used. While it is true that advanced machinery and processes can be beneficial for making consistently high-quality pianos, the highest level of refinement cannot be achieved without the contribution of skilled artisans. This skilled handwork process will live on in our industry for the benefit of those pianists who wish to make music at the most refined levels.
Don Mannino is Director of Field Services for Kawai and Shigeru Kawai Pianos.
Computerized Manufacturing Inadequate for High-End Pianos
by Udo Steingraeber
Even as one of the few high-end piano makers, we agree with most of our colleague Frank Emerson's arguments and passionate plea for computer-aided design (CAD) and computer-aided manufacturing (CAM). Let's start with praise for their big contribution: Computer numerical control (CNC) manufacturing has brought efficiency and precision to the piano-manufacturing process. At the same time, I am absolutely certain that the very best CNC-manufactured pianos will never be able to crowd out the market for hand-built pianos.
Which hand-built pianos are we referring to? About which musical needs, and from which customers, are we speaking? I would like to talk about the high end only: high-end players, high-end listeners, and high-end instruments. This small piano market ranges from David Rubenstein's (Los Angeles) one-man show, with his astonishing 12' 2" model R-371, to Steinway & Sons (Hamburg), the world's market leader in concert pianos. But in this tiny market, where hand building is still part of the production process, there are more manufacturers today than there were 20 years ago! Obviously, there is a market and a need for high-end pianos for high-end pianists. It's true that this market is only around 1% of total piano sales, but these are the instruments with which 99% of the world's concerts and recordings are produced; only these few pianos can enable artists to create their very best music and high-end interpretation.
It's always worth checking the processes to learn where CAD and CAM are as good as hand-built — and to know where they are not adequate replacements. Here at Steingraeber & Söhne, in Bayreuth, we would be fools if, for example, we built the lyre of our model E-272 concert grand by hand and not with CAD/CAM — but it's equally true that we would be idiots if we used CAD/CAM to prefabricate the ribs of our E-272 soundboard instead of shaping them after we had glued them to the soundboard. In this example, it may seem as if we are working the wrong way 'round, but with our old-fashioned way, which stretches the board and crown, the wood will get additional inner tension. This is only one example of many in the building of high-end pianos where the application of a master's hand creates dynamic ranges, partials, volume — in a word, music, and not just percussion or, even worse, noise.
During the last ten years, Steingraeber & Söhne has brought five new models to the market, and CAD was used in the development of all of them. Even the Department of Experimental Physics at the University of Bayreuth, with its computer programs and laboratories, took part in the research. But the sound of a piano is multi-causal, which makes impossible the design of a piano in its totality by mathematical procedures and physical descriptions. In the end, in every high-end construction design, the empirical method must join CAD; there are simply too many sound sources, materials, and interactions involved in the sound-creation process.
Yes, our modern piano has a lot of machine-like features, mostly developed in the 19th century. This enables assembly-line manufacturers to regard it as an industrial product, a bundle of modules that can be prefabricated and then assembled. If this is well done, the result can be very good, and suitable for rehearsal pianos up to a reasonable or even high standard — but not up to a concert-level standard, which requires a richer variety of sound colors. These depend on the activation of not only the primary sound sources of soundboard and strings, but of the secondary sound sources, that is, the vibration of the entire instrument, within the dynamic process of sound production. Creating secondary sound sources is the major goal of master builders, and often stands diametrically opposed to the pragmatic wishes of production managers, and the characteristics of modern materials such as medium-density fiberboard (MDF). Though modern materials and processes may be convenient for use in CNC manufacturing, they often inhibit the creation of secondary sound sources; and woods like spruce, with their unpredictable natural variations, often do not permit standardization of the production process by computerized machinery.
We at Steingraeber do not like being part of a geriatric phase of the piano industry, and thus we are always innovating. In cooperation with partners like Richard Dain, Renner, and others, in the last five years we have brought out carbon-fiber soundboards, the Phoenix design with bridge agraffes, adjustable hitch pins, and the fast-repeating SFM action for upright pianos. We are offering half-blow and — brand new — Sordino (celeste) pedals, and in 2013 will introduce the newly developed Renner-Steingraeber-Alu-Action. We are a vigorous member of the music world, manufacturing 120 to 150 pianos per year. We will always keep our eyes open to using CAD/CAM wherever possible, without reducing the high quality of our instruments — and we will never stop using our hands when it helps.
Udo Steingraeber is owner of Steingraeber & Söhne, a piano maker in Bayreuth, Germany, since 1852.
Emerson responds:
In response to the arguments in support of production by hand, I find nothing with which to disagree. I would only like to clarify my arguments in support of the use of modern technologies in the production of pianos.
Most piano salespeople would agree that there is no shortage of consumers who begin their search for a piano looking only at the price tag, seeking the least expensive piano they can find. There will always be a market for that. At the other extreme, there will always be a market for those who require the absolute best that money can buy.
Anyone who has worked in product development knows that it is fairly easy, and not terribly costly, to get from the lowest level of quality to one just a little bit higher. However, the closer you get to the highest level of quality, the more difficult and more costly each additional increase in quality becomes, until you reach a point of diminishing returns. If we could quantify the value added for each additional dollar of cost and plot the results in a chart, we would likely see a variation of a normal bell curve, with a long, gradual taper at the high-quality end of the scale. Modern technologies have broadened the peak of that bell curve, lengthening the span over which spending additional dollars results in a marked increase in quality before the point of diminishing returns is reached.
Any business must contend with competing priorities. Piano manufacturers should always be engaged in maintaining and improving quality, but must also keep down costs to remain competitive. The traditional assumption is that reductions in cost are always at the expense of quality, and that the key to success is finding a balance between the two. However, modern technology offers many opportunities to defy the traditional assumption that cost and quality must always be at odds. Trading off man-hours for machine time can often reduce costs, but can also improve the consistency and quality of a finished part. The cumulative impact of many such solutions is a higher-quality product at a lower cost, which translates into a broader peak in the bell curve of value-added vs. cost-added.
This is not to say that technology is the solution to every problem. But we're headed in that direction, and it's certainly not fanciful to suggest that, in the not-too-distant future, most of the piano-manufacturing processes that today must be done by hand will instead be done by machines, and at a higher level of quality for lower cost.