These innovations, which collectively define the modern grand piano, also made it difficult for small piano workshops to flourish — they couldn't afford the cost of tooling up for iron-plate casting, for instance, or manufacturing the many small parts that make up a modern piano action. By the beginning of the 20th century, workshop-based piano builders had virtually disappeared.
For several decades in the 20th century, most of the larger piano makers cast their own plates, bent their own rims, glued up their own soundboards and pinblocks, and manufactured their own action parts. Some makers took such vertical integration to the point of owning their own forests and sawmills. Now, however, in the 21st century, specialization has once again become commonplace. Although a few of the largest piano manufacturers still produce virtually all parts for their pianos, most purchase action parts and hammers from companies that specialize in such components, soundboards and pinblocks from a wood-products firm, plates from a foundry, and so on. Along with this specialization, a remarkable breed of craftsperson has begun to build high-quality grand pianos in a workshop setting, defying the conventional wisdom that pianos must be made in large quantities by large corporations.
One of the earliest of these maverick piano makers was Mark Allen, who, starting about 1970 in Philadelphia and then Portland, Oregon, built three concert grands. What drives a person to venture into a world as risky and difficult as piano building? "I came to build a concert grand," Allen said in a 1982 Connoisseur magazine interview by Gary Graffman, "because I spent all my adult life working with pianists. In my own way I became a connoisseur of this thing, the piano. And I decided what the ultimate instrument was. It was an even, balanced scale. It must be unobtrusive and subtle when you want it so, and powerful and brawny when you want that. It would have the singing quality of the human voice." Although he enjoyed a small measure of success after being featured in a few magazine articles and when noted pianist Cyprien Katsaris bought one of his instruments, Allen ultimately left piano making, and today runs a piano-restoration business in North Carolina.
Some of these "boutique" shops build their instruments using components — soundboards, rims, pinblocks, plates — from specialist companies, while others insist on making nearly everything themselves. Most of these builders will complete, in a year, roughly as many instruments as, say, Steinway or Bösendorfer — their own instruments largely handcrafted — will finish in a day.
David Rubenstein, Los Angeles, California
"Actually," says piano builder David Rubenstein, of Los Angeles, "it's more a question of how many years per piano than how many pianos per year!" Rubenstein, who works mostly alone, has built only two instruments since he began in 2002. He builds two models, a 12' 2" grand ($325,000) that is currently the world's largest commercially available piano, and an 8' grand ($175,000). The larger instrument has 97 keys, extending the bass to the C an octave below the lowest C of a standard 88-note keyboard. A musician and potter by training, Rubenstein says, "I originally wanted to make pianos because they are beautiful. My current feeling is that there are pianos I would like to see and play that won't exist unless I make them."
Rubenstein says that, except for the stringing scale, he designed the entire piano himself. He also built the rim and rim presses, and even made the veneer used in the rim. "I make my own keyboards and keyframes," he says, "and also offer this service to technicians and rebuilders." Rubenstein makes his own soundboards and ribs from rough lumber. Although he has sometimes made his own pinblocks, he generally uses blocks made by André Bolduc, of Canada. Currently, most of the action parts and hammers he uses are made by the German firm of Louis Renner.
Rather than using traditional cast iron for his pianos' plates or frames, Rubenstein designed a steel plate welded together from pieces cut by CNC waterjet. "My instruments are truly one-off products, and my system of steel-plate making permits a wide latitude of design possibilities not possible with cast iron," he says. "These are just a few things that distinguish me from all other piano makers, be they large concerns or other boutique makers."
Luigi Borgato, Italy
If it's the fabricated steel plate that sets Rubenstein's instruments apart, for Luigi Borgato it's the fourth string. The 49-year-old Italian maker builds large grands featuring four strings per treble note, instead of the usual three. The idea for the fourth string, he says, was suggested by Beethoven's request for more strings in the treble of a fortepiano built for him by Viennese builder Conrad Graf — an attempt to overcome the composer's growing deafness by getting more sound out of the instrument.
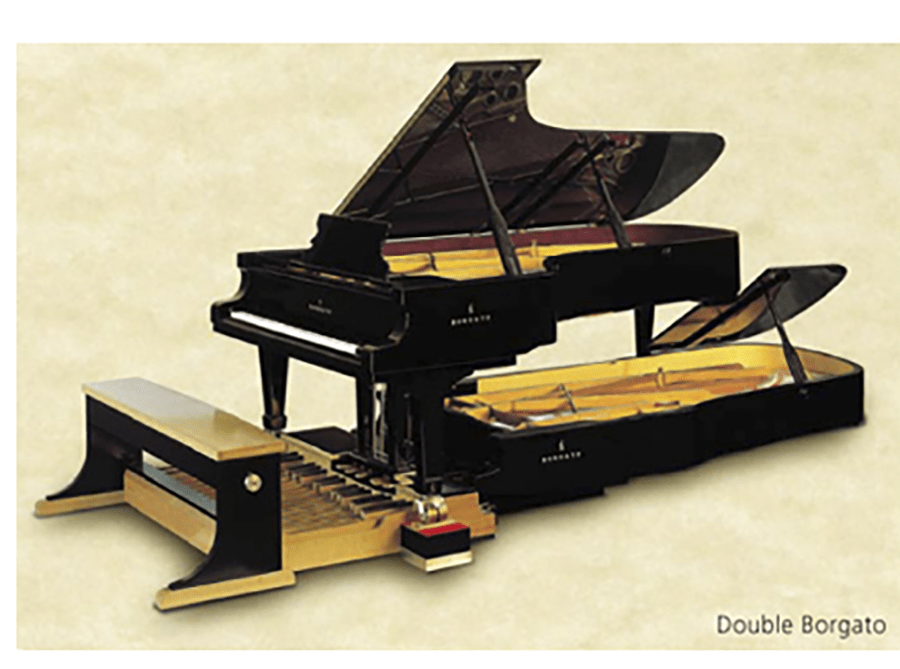
Another historical idea inspired Borgato to build a pedal piano — actually, two instruments played by one player — so that works composed for pedal piano by Schumann and Liszt, among others, might be performed and heard as their composers had intended. Borgato's version stacks his 9' 3" concert grand atop a 13' instrument fitted with 37 pedals similar to those found on an organ. A piano technician by training, Borgato finished his first piano in 1991, and continues to build his instruments one at a time — a process that, he says, takes 1,120 hours per piano. As one would expect for such handcrafted instruments, Borgato's pianos are expensive: the Model L 282 Grand Coda costs more than $200,000, and the Double Borgato runs over $320,000 (both prices before taxes).
The Australians: Wayne Stuart, Ron Overs
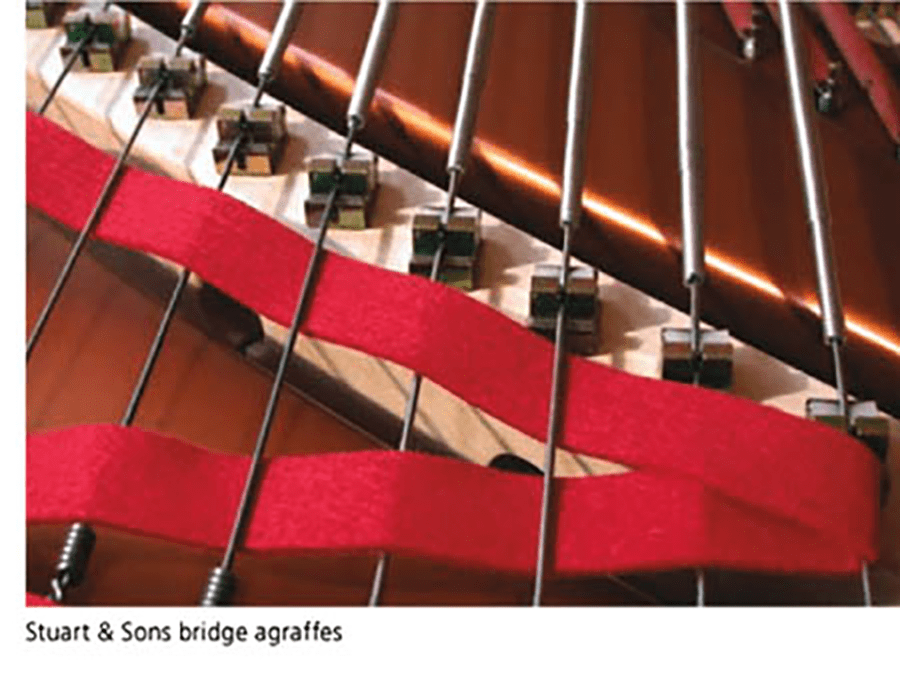
Wayne Stuart, an Australian piano designer and builder who trained as a piano technician in the 1970s, makes pianos with bridge agraffes: metal fixtures that connect the strings to the bridge and keep the vibrations of the strings in the vertical plane (see Photo 5). While most grand pianos use agraffes at the front end of the strings, their use at the bridge end has, historically, been rare. The strings in most pianos are fastened to the bridges by means of angled bridge pins, resulting in a string vibration pattern that begins in the vertical plane but then changes to the horizontal, which causes an audible shift in tone as the sound dies away. According to Stuart, "The bridge agraffe liberates the soundboard from the reaction forces produced by bending the wire at the bridge termination position. This design enables the soundboard to be fabricated along the same principles as loudspeakers. The soundboard is no longer a load-bearing structure but, rather, a light, stiff diaphragm that responds to a much broader set of string motions, and thus increases its dynamic potential."
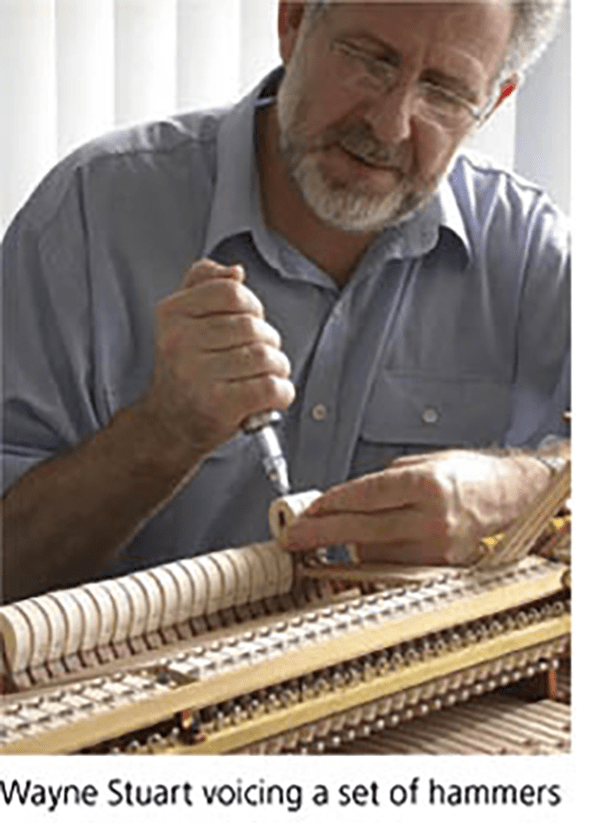
Stuart's instruments sport, in addition to the traditional three pedals, a fourth that reduces the travel distance of the hammer and key levers. "This is a significant addition for the player, particularly in accompaniment and where textural effects and control over tone color are sought," says Stuart. "This pedal can be used independently, or simultaneously with the shift pedal to produce the most extraordinary effects." The Stuart & Sons piano comes in two sizes, a 9' 6" concert grand and a 7' 2" studio grand, each with options of 97 or 102 keys. The 102-key model ranges from the C an octave below the lowest C of a standard 88-note keyboard to F above the top C of a standard keyboard. Prices of Stuart's instruments range from $150,000 to $300,000 before taxes.
Another Australian, Ron Overs, has built a small number of pianos emphasizing other features. One is a soundboard with ribs shaped like small I-beams, which Overs says helps the soundboard retain its crown because they are nominally 60% stronger directly under the bridges than are conventional soundboard ribs. Another is his proprietary action mechanism (patent pending), which has "approximately half the friction of any other roller action you would care to compare it to."
Delwin Fandrich, Olympia, Washington
Back in the U.S., piano technician and designer Delwin Fandrich is working on a new piano that he calls "my interpretation of a direction piano development might have taken had we not allowed ourselves to be caught up with the notion that bigger and more massive is always a good thing." Inspired by the fortepianos of the mid-19th century, the new instrument is 8' 2½" long, but, being narrower, takes up about the same floor space as a conventional 7' 4" grand, according to Fandrich, and is about one-third lighter. He calls his new creation "my interpretation of those wonderful transitional instruments that appeared roughly between 1840 and 1870. It is not a reproduction of these instruments, but a thoroughly modern instrument; indeed, it is one of the most technologically advanced pianos available today." Fandrich's new piano will feature low-tensioned scaling, lighter hammers, and the new composite action parts from Wessel, Nickel & Gross.
Michael Spreeman, Scottsdale, Arizona
What attracted Scottsdale piano technician Michael Spreeman to piano building was simply the potential to "design and create something exceptional," he says. "In a business society that seems to be focused on building things faster, for less money, and in greater quantity at the expense of quality, I wanted to move in the opposite direction and exist in a different head space." Working with two employees, Spreeman builds two to six pianos a year, using rims and plates made in Germany by Sauter. "Everything that has to do with production of sound is our exclusive design," he says. "This includes the soundboard, rib scale, bridges, and string scales." Spreeman's pianos come in two models, the 7' 3" Model 220 and the 9' Model 275, and bear the name Ravenscroft, in honor of local jazz pianist Bob Ravenscroft.
Although the sources for some of Spreeman's materials can change depending on the specific piano he's building, a typical Ravenscroft 220 (base price $230,000) might have a keyboard from Kluge, and action and hammers from Renner, both German companies; a red-spruce soundboard panel from Ciresa, in Italy; and a pinblock from André Bolduc, in Canada. "The sound I offer," says Spreeman, "is a bit of a hybrid. I am after a pure European clarity with an American sort of fullness and color. We also obsess over the actions. Each action is CAD optimized, meticulously assembled and regulated, and weighed off to one-tenth of a gram from note to note. We strive to make the interface between the artist and the piano as invisible as humanly possible."
Spreeman could easily be speaking for all his fellow boutique piano makers when he says, "We don't mass-produce a ‘product.' Each piano we build is the best we have to offer. Once completed, they are evaluated by my team, and by artists who provide feedback about performance. We then take these evaluations, assess them, and implement design changes to further enhance the next piano. My primary focus is to design a piano that allows artists to express themselves in ways they've never been able to before, and for listeners to experience this expression with the purity and fullness of that artist's intent."
Or, as Luigi Borgato puts it, these boutique pianos "have the charm of authentic works of art that reveal the inspiration and passion from which they were designed. Exaltation of matter, perfection of form, care of every little detail. These things make the instruments unique — created by hand, one by one."
Contact List
Luigi Borgato
info@borgato.it
www.borgato.it
Delwin Fandrich
del@fandrichpiano.com
www.fandrichpiano.com
Ron Overs
sec@overspianos.com.au
www.overspianos.com.au
David Rubenstein
dr@rubensteinpianos.com
www.rubensteinpianos.com
Michael Spreeman
Michael@spreemanpianoinnovations.com
www.Ravenscroftpianos.com
Wayne Stuart
sales@stuartandsons.com
www.stuartandsons.com